

On the flip side,inflexibility is a major barrier to standalone charge management ICs intoday's rapidly-changing battery world.
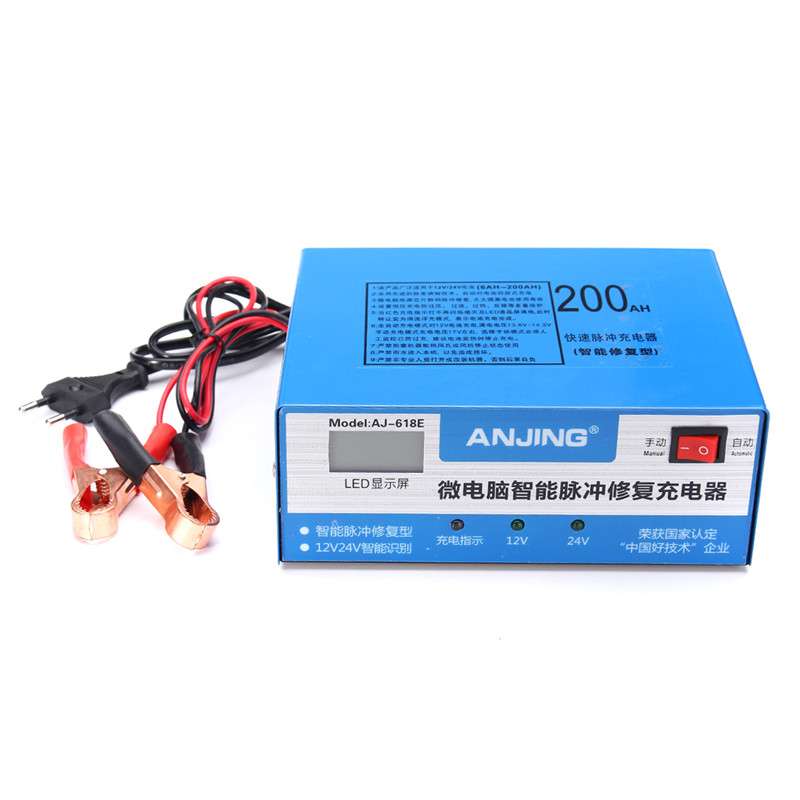
#LITHIUM BATTERY PULSE CHARGER SOFTWARE#
This saves time-to-market and reduces cost by shortening developmenttime and eliminating software development.
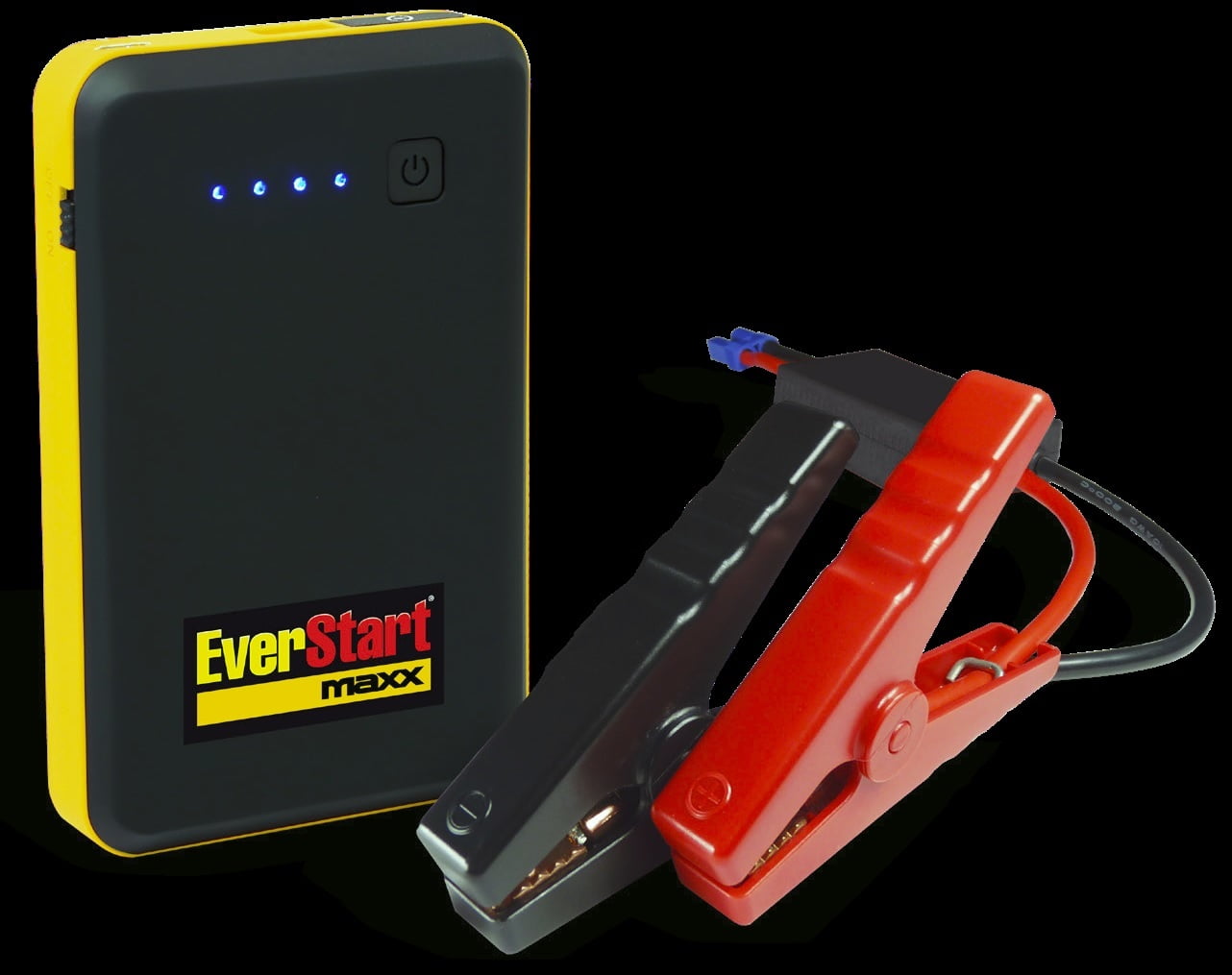
Semiconductor companies typically deliver good product support inthe form of detailed datasheets and application notes to help designersimplement the battery charger IC into the system. Since thecharge algorithm and housekeeping circuits are built into the IC, nofirmware is required and the design is straightforward.įigure4: The required PCB space and associated components are minimized whenusing an integrated battery-management controller. Thus, therequired PCB space and associated components are minimized when usingan integrated solution.įigure 4 below shows atypical application circuit when a fully integrated battery managementcontroller is applied as a stand-alone battery charger. The stand-alone Li-ion battery charger IC, especially for the lineartopology, may require only SMD capacitors to maintain AC stability andprovide compensation when a battery load is not present.

The main reasons that designers select fully integrated, single-chipbattery charge-management systems are compact size, low cost andminimum design time/effort/ resources. The system continues monitoring the battery voltage and rechargeswhen it falls below the recharge threshold voltage, to limit the numberof charge/discharge cycles and prolong the battery's life, whilekeeping its voltage at a safe level.įigure3: A typical charge profile of an MCU-directed PWM controller for asingle-cell 1700mAh Li-ion battery with CC-CV algorithm at 1A chargerate is shown. Thecharge termination value in this example is 200mA. Once it passes the pre-conditioning stage, the system goes intoconstant-current stage until a regulated voltage is detected. The algorithm starts withprecondition if the battery voltage is below the pre-conditioningthreshold. Thefollowing equations show the calculations for linear and switchingpower dissipations that are applied in the above example:įigure 3 below depicts atypical charge profile of an MCU-directed PWM controller for asingle-cell 1,700mAh Li-ion battery with constant current/constantvoltage (CC-CV) algorithm at 1A charge rate. SEPIC is a switching topology that deliversbetter efficiency and less power dissipations when I/O voltagedifference is wide and current flow is significant.įor example, operating a 9V input voltage when VBAT is 4V andICHARGE is 1A, the power dissipation for popular linear solutions is(9V – 4V) * 1A = 5W and the same condition for a switching solutionwith 90 percent efficiency is only 4W * (0.1/0.9) = 0.44W.Ĭooling a 1/2W solution is much easier than cooling a 5W system. If flexibility is important for product development and the ability tomake changes during a project is necessary, then an MCU directed PWMcontroller battery charge-management system is a perfect fit.įigure 2 above demonstratesa typical single ended primary inductor converter ( SEPIC)topology multicell, multichemistry charge-management system using a highvoltage PWM and ageneral purpose 8-bitMCU.Īdvanced MCUs are available for GPIOs and ADCs for additionalsensing and output status. Thus,reliability should always come first when designing a product, ifperformance is the trade-off.įigure2: A typical SEPIC topology multi-cell, multi-chemistrycharge-management system using the MCP1631 high-voltage PWM and thePIC12F683 general-purpose MCU is shown. Although it is not true in allapplications, saving space by creating highly-integrated solutions maycost more than a system built from discrete components. The short time permitted from concept to final product alsominimizes the resources used and reduces cost by saving design time.Īdditional components may result in extra failure factor points and,in some cases, increase in costs. Time-to-market is significant forconsumer products that have a short product life cycle.įast response to market changes is important in today's fast-pacedworld. Production challenges are often associated with time-to-market,total system cost and reliability. Battery manufacturers recommend undercharging a 4.2V regulatedLi-ion battery at 4.1V to extend its life for backup energyapplications.
